The concept of an Alde closed glycol system is intended to explore how the system could be modified to eliminate or at least greatly reduce the glycol's contact with air containing oxygen. The life of the glycol and corrosion inhibitor would be greatly improved if oxygen is eliminated or minimized according to the National Sales Representative of one of the glycol suppliers I have spoken with.
There are some specific hardware modifications that would be required, but I suggest discussion of the basic concept along with the pros and cons before trying to solve all the details.
One thing that needs to be understood is the expansion and contraction of the system glycol and trapped vapor in the system caused by the temperature changes the system will see. This can be calculated if glycol and vapor volumes are known along with the temperature extremes the system will see - max and min. Once the tank cap is placed on the tank, there must be sufficient vapor volume in the bladder to make up the volume change of the glycol as it contracts based on the minimum temperature plus the vapor volume change due to the same temperature change.
The glycol tank is the focal point since the current vents to atmosphere and the fill cap are here. The tank I have has two tubing connections and the cap - one is a vent which is routed down into the area beneath the seat and the other is a glycol overflow which is routed down and through of the trailer floor.
Option 1:
The simplest conversion to a closed system would be to simply route one of the vent lines to an inflatable bladder and cap the overflow line. Any remaining oxygen in the air remaining in the tank and bladder would get absorbed by the glycol and consumed but no additional oxygen could enter until the tank cap is removed again.
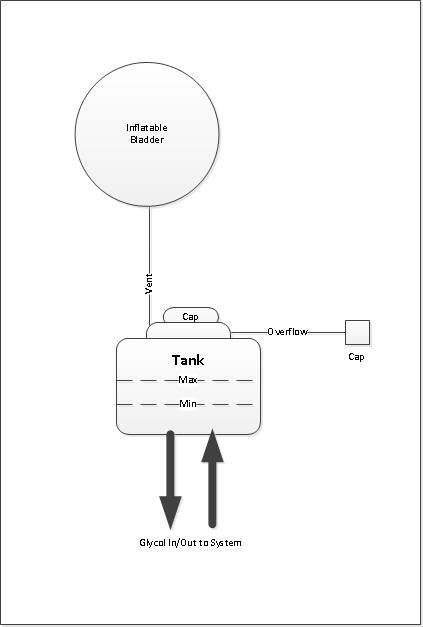
Pros
Cons
- No way to eliminate residual air with oxygen in the tank vapor space when tank cap installed
- Sizing of the bladder to accommodate glycol expansion and contraction based on max and min temperatures. The
bladder should not cause an increase in glycol tank pressure as it inflates so
as not to increase the likely hood of glycol leaks, blowing the cap off the
glycol tank or even worse, splitting the tank open.
- Ensure correct volume of air is left in bladder to accommodate min temperature when closing tank cap
Option 2:
By adding
valves to the vent and overflow lines would allow purging air with inert gas from the glycol tank and bladder. Purging
would be performed after opening the tank cap to fill the system with glycol or
check the glycol pH each year. This would improve the effectiveness of
eliminating oxygen exposure to the glycol:
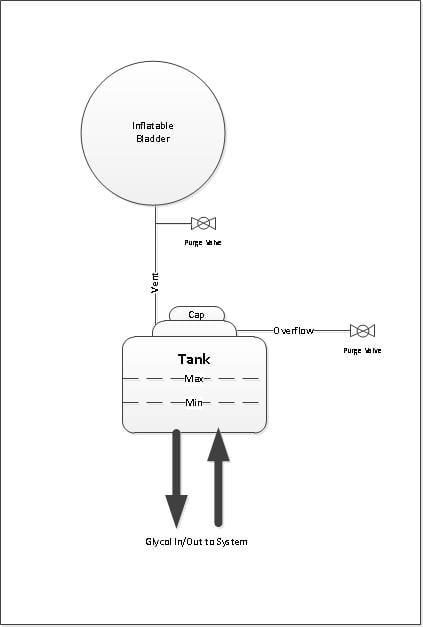
Pros
- Still very simple and not much additional cost
Cons
- Sizing of the bladder to accommodate glycol expansion and contraction based on max and min temperatures. The bladder should not cause an increase in glycol tank pressure as it inflates so as not to increase the likely hood of glycol leaks, blowing the cap off the glycol tank or even worse, splitting the tank open.
- Ensure correct volume of inert gas is left in bladder to accommodate min temperature when closing tank cap
- Securing a convenient source of inert gas especially when traveling if glycol had to be added for some reason
Option 3:
Due to
space limitations (at least in my trailer), the bladder must be located below
the glycol tank. Provision should be
made to prevent any glycol getting in the small diameter tubing to the bladder
which could be pushed into the bladder.
This could be by simply installing a larger diameter tube or hose
section in the vertical tubing run from the tank vent before it turns down to
the bladder. Glycol entering this larger
diameter would not tend to be pushed along the tube in the vertical.
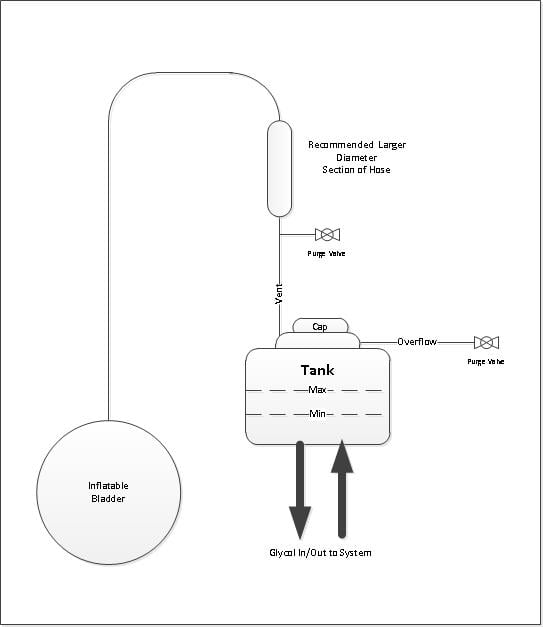
Pros and Cons same as Option 2.
Option 4:
The addition of a method of preventing a vacuum or over pressuring of the glycol tank would remove all the concerns with the max and min temperature swings.
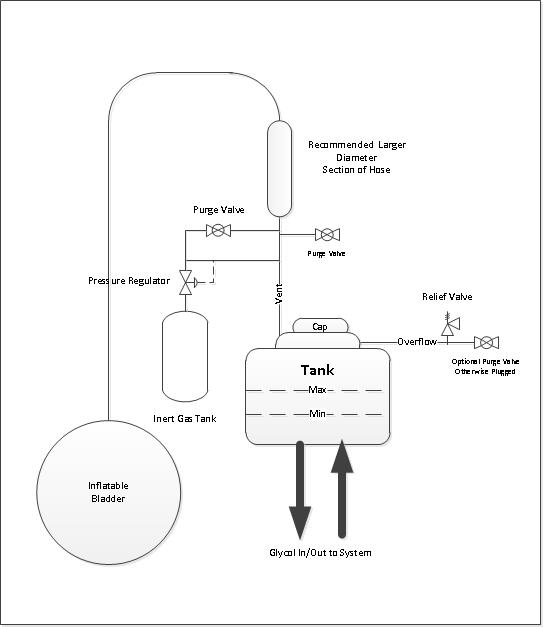
Pros
- Automatic Protection against over pressurization and vacume
- Eliminates air with oxygen once purged
Cons
- More complicated and costly
- More valves and line in congested spaces
I am sure I have miss something in the above and maybe there is another option I have not identified. Any coments, additions or suggestions are invited.
Comments
Check out this 100% No Water thread.
At least one owner has made the 'custom' conversion.
TV: '17 Colorado V6 Z71 4x4, Tow Package, GM Brake Controller
Adventures: 56 Nights: 379 Towing Miles 47,220
I'm not sure if your comment about the "one custom conversion" refers to the switch to the waterless fluid or the Seaflo accumulator installed by Dalehelman to make a closed system similar to the Option 3 I showed.
I for one would be very hesitant switching to a totally different type of heat medium fluid due to unknown material compatibility questions with all the components in the Alde system. Switching to a true heat medium "oil" sounds great except for the toxicity issues along with material compatibility issues also. Years back I did install a hot oil system in a facility.
With that said, I just switched to a different glycol in my trailer after researching many brands but did not use Rhomar. So, I am willing to try something new to an extent but with the only variable around the corrosion inhibiter used in the glycol.
I really like the use of the Seaflo installed to make the system a closed system with two questions:
1. Is the volume large enough to account for expansion (which apparently it is based on that conversation) and possible contraction in low temperature environments?
2. No provision to purge with inert gas which improves the amount of air exposed to the system fluid - ie glycol.
But I do agree that the glycol/water mixture can absorb oxygen from the air. According to the glycol manufacturer's National Sales Rep I spoke with at length, he confirmed elimination of air containing oxygen is a very desirable thing to improve the life and corrosion protection performance of the glycol.
Years ago I worked with a hot oil system in a facility. Don't remember the flash point of the oil, but I am pretty sure it was considered toxic and not recommended for use in a system that could have contact with a drinking water system. This is why ethylene glycol used in automobiles is not used in these type of systems too.
While trying to sleep last night I realized the key to making this work is to make sure the bladder is sized properly, is reliably available, not expensive and can be used to acquire nitrogen for purging the system. Hence Option 4.
Option 4:
Since the total volume of the glycol tank is so small (maybe ½ gallon or so, the total expansion/contraction for the maximum and minimum temperatures cannot be more that a fraction of the total tank volume. No need for any detailed calculations. Just make sure the bladder is at least as large as the glycol tank. To support this assumption, consider how much the glycol level rises in the tank going from say 60 F to 180 F when in use for heating. I think the glycol level in the tank only raises an inch or so. Therefore, if a bladder with a volume about equal to the total volume of the glycol tank is selected and left only ½ filled (ie no positive pressure), there should be ample volume to account for glycol expansion or contraction. My gut feel tells me this is even conservative.
If a small tire inner tube is used for the bladder – maybe like the size for an ATV, it could be filled with nitrogen at a local tire store then connected to the glycol tank and deflated until it is about halfway flattened out with the purge vent open to displace the air in the glycol tank. The remaining nitrogen in the inner tube after plugging is then available for glycol contraction and the flatten portion of the inner tube is available for glycol expansion.
The glycol life should be extended along with the corrosion inhibitor in the glycol if the system was closed. Another pro is the pitting of aluminum under the rubber hose connections MAY be eliminated.
One potential con is by eliminating oxygen in the glycol, corrosion and crevice corrosion of stainless steel may be a problem which could impact the connection to the Alde unit.
For now, until I learn more, I will keep my system open in hopes of avoiding any problem with corrosion of the stainless steel in the system which would be more costly than the possible glycol life extension. I coated the ends of my aluminum convectors with epoxy and replaced all the connectors with stainless steel. I am hopping the coating of the convector ends solves the aluminum corrosion under the EPDM rubber hoses and by keeping the system open hopefully will avoid problems with the stainless steel.