I have finished my modification to add a supporting bracket that secures Dale Helman's scissor jack mounting adapter plate to the full length of the trailer frame extensions by bolting directly to the frame using all three mounting bolts, as provided by NuCamp.
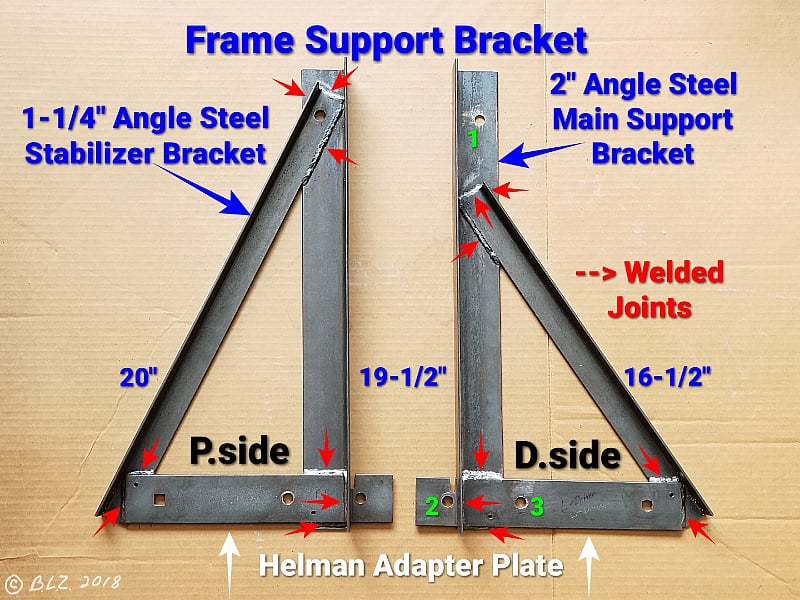
Here's a view of both right & left brackets made by adding two angled structural steel pieces to the adapter plate and welding all three together where they overlap, to create a single rigid triangular bracket. The main 2x19.5" piece is drilled for bolting directly onto the angle trailer frame extension using the existing stud mount plus the other two existing studs going through the adapter plate which holds it tight against the frame over its entire length. The two brackets are made different, as explained further in a photo below.
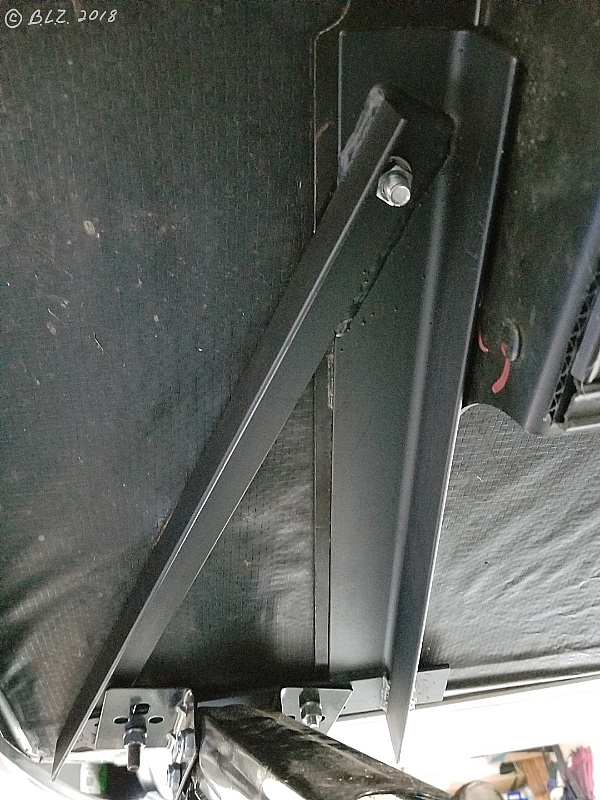
Above is the installed bracket, after painting, plus jack. Note how the main support piece bolts directly over the trailer frame, while the angled piece adds support & rigidity to the previously floating end of the adapter plate, transferring its load back to the trailer frame.
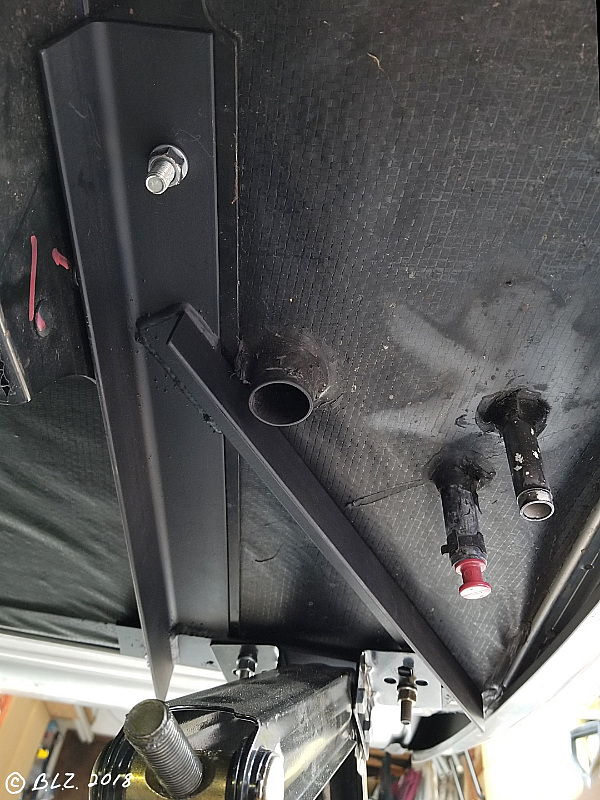
Because of the drainage tubes exiting through the drivers side floor nearby, it was necessary to shorten the angled piece rather than bolting it to the forward end. This is no problem though, because it is firmly welded to the main support.
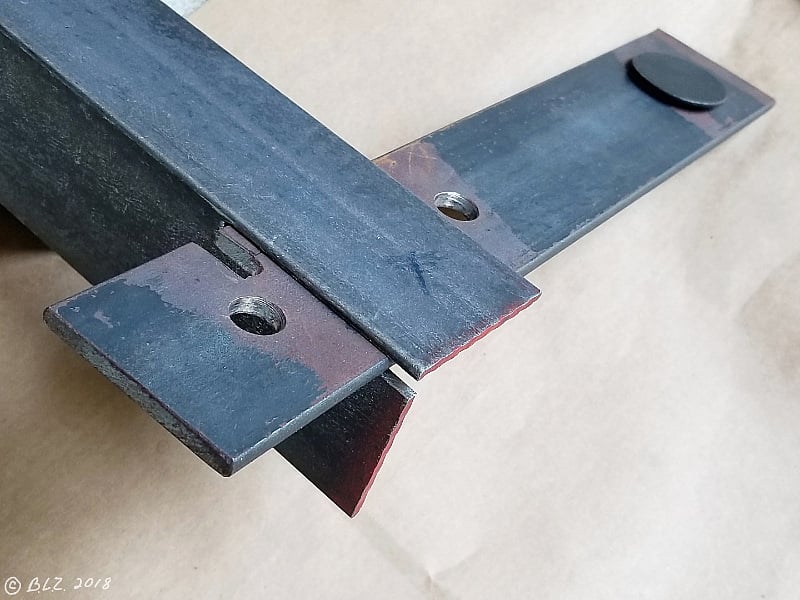
This shows how the adapter plate fits into a slot cut into the main angle support. This slot lends additional support to the adapter plate by resisting potential tilting from the leverage created when the jack pushes up on the opposite end.
It was a bit challenging, but necessary, to keep the hacksaw blade flat against the inside surface of the angle steel while making the first cut for this slot, in order to leave a flat inner surface without a lump so the adapter would lay flat. I tried, for a snug fit & greater strength, to make an accurate second cut without leaving too wide of a gap in the slot; but again, this joint will be welded on three sides anyway, including over the length of the slot.
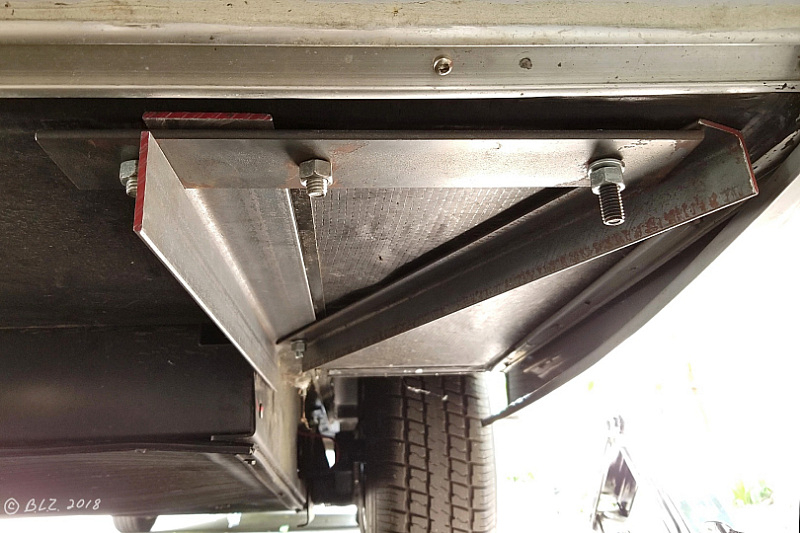
This shows how the parts all fit together before being welded. It was remarkably strong even before welding, so we actually used it like this for leveling while camping before actually getting any of the pieces welded.
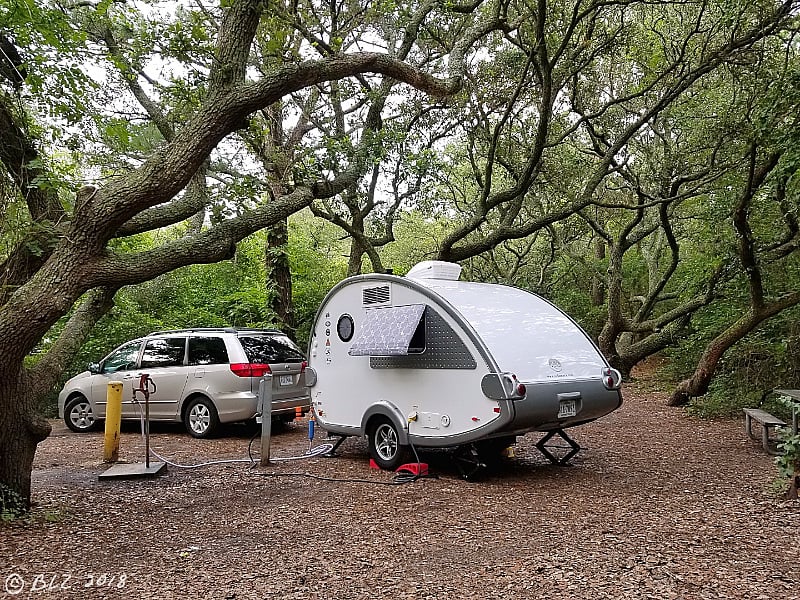
Here you can see the passenger side jack using the new frame support bracket for leveling while camping (before welded together).
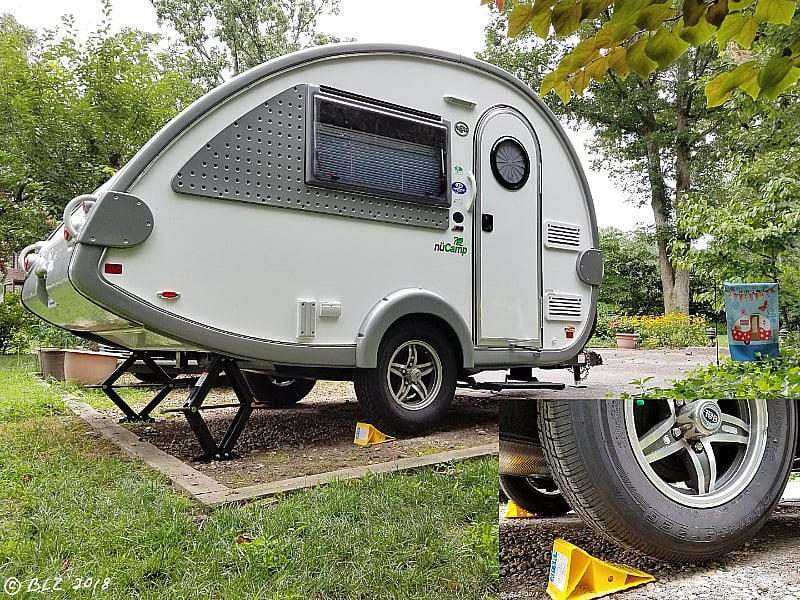
As a final test for strength of the newly welded brackets, I dropped the tongue down (slightly uphill at tongue), raised the rear jacks a bit higher than needed for leveling (a bit more on passenger side which is slightly downhill) , then raised the tongue jack until the passenger side wheel was about an inch or more off the ground to simulate conditions for changing a tire. It remained very stable, and the bracket was still very solid with no observed changes.
I now feel confident in using these jacks for both leveling and wheel or tire maintenace & repair.
Use this idea at your own risk, of course, and sorry, but no, I would not want to make any more of these. 😉 Probably best to test fit everything to the trailer as you go anyway, so you can mark exact final positions of the overlapping frame members. I would also suggest doing what I did before welding..
I got mine welded at a local shop for $20, but first I drilled a small hole (1/8"?) in each of the three overlapping corners & used 3 small bolts to hold it all securely together temporarily until welded, so as to maintain the exact position of each piece. You can see some of those holes in the first photo.
Comments
Wouldn't it be easier to simply move the jack inboard until it is directly underneath the corner of the frame?
TV: 2005 Toyota Sienna LE (3.3L V6)
RV: 2018 T@B 320S, >100 mods
I was really just wanting to have the ability to do a bit more than just minor leveling of the trailer, while still maintaining a certain level of personal comfort, and to be able to lift the wheels off the ground if ever needed without having to use a separate jack.
I also hope that I'm not causing any worry for anyone already using @Dalehelman's adapter plate, as it seems to have already proven itself for what he intended to use it for. I do still appreciate the way it puts the jacks closer to the side & angled outwards so they are easier to reach than the original stabilizers were in back.
TV: 2005 Toyota Sienna LE (3.3L V6)
RV: 2018 T@B 320S, >100 mods
Update:
After probing both sides of the jack mounts on the currently leveled & stabilized trailer, here's what I found.. There is space above the corners (Scott's arrow) of both outer angle brackets, between them and the trailer floor; however, after probing further that appears to be because the tops of the two elevator bolts used to mount the jacks are slightly thicker above the plate than the angle bracket, because they appear to be tight against the wood beam inside the floor. So, clearly, the outer corners are not suspended as far as supporting all the weight under load, but how much of the load is redistributed by the bracket versus resting on the wood crossmember is still unknown at this point.
TV: 2005 Toyota Sienna LE (3.3L V6)
RV: 2018 T@B 320S, >100 mods
TV: 2005 Toyota Sienna LE (3.3L V6)
RV: 2018 T@B 320S, >100 mods
BrianZ, I like your triangle arrangement.
I am thinking of building some stouter jack top side plate angles that will be stiffer and allow new choice of bolt hole locations. I am concerned with the jacks all the way up, the back of the jacks stick out and hang down reducing ground clearance substantially. Keeping the jack lift centered over the frame but forward of the rear bolt locations, and angled to the outside at the rear may improve ground clearance. More research is indicated.
TV: 2005 Toyota Sienna LE (3.3L V6)
RV: 2018 T@B 320S, >100 mods
Clearance may not be a real issue but the originals were tucked in soo nice.