Check your T fuses with an infrared thermometer while under Inverter load.
As part of an electrical upgrade, installed a Blue Sea 225amp T-fuse on Blue Sea holder between new 2000w inverter and new Blue Sea rotary isolation switch.
All 3/8" terminals were initially set with a torque driver to 35 ft-lb which seemed very light; hand tightening averaged 55-75 ft lb which I ran with.
Operations testing with infrared heat gun monitoring elicited
severe heating at one fuse terminal closest to Inverter. Ambient 76F, wiring 76-78F, and terminal climbed to
147F. Shut it down, removed, inspected. Good mating of surfaces, good torque, no interferences from heat shrink. Good lug crimp. Wires closest to inverter did not heat up at all. Tight bend in photo is undesirable but did not create an issue.
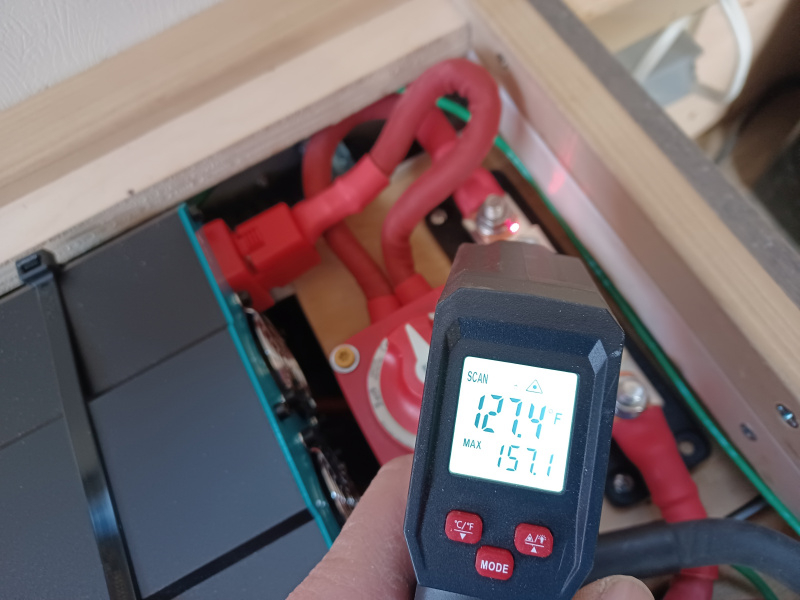
Here is what I saw on removal: apparent coating on the T Fuse lug surfaces- either a lacquer or shop oxidation; and transfer of this surface material to mating surfaces on the (chromed?) Fuse holder. Compare with the bare metal exposed by the serrated lock nut.
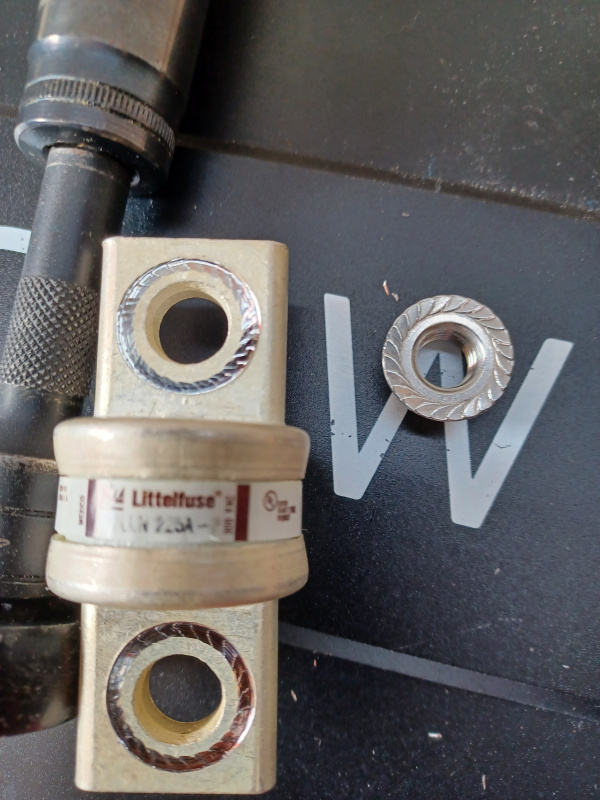
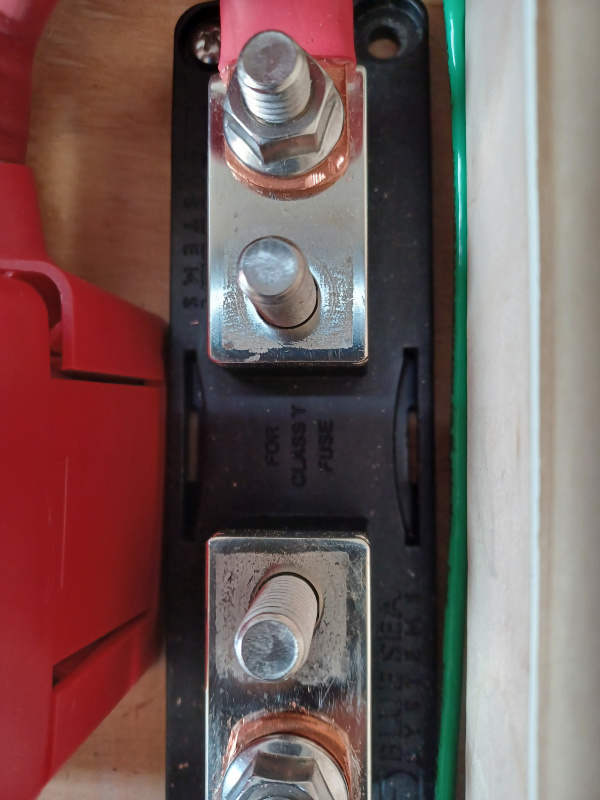
I sanded ALL surfaces with 400 grit paper, reinstalled and torques, and tested satisfactorily.
Nearly NO heat rise. Thank goodness.
Quite clearly this coating on the fuse was creating enormous resistance!
I have written to Blue Sea technical support querying what coating they use if any, and whether they have encountered counterfeit materials for sale on
Amazon where I bought this.
I am not happy with the Blue Sea fuse holder: the terminal posts are embedded in plastic and are NOT BONDED to the plates. Looking straight down at end of terminal bolt you can see a slight gap between it and the terminal plate.
Strangely the hot point was at the terminal nut points closest to the fuse on the 'outbound' inverter side. The opposite side of nut was far less hot, and adjacent surfaces barely hot at all. This suggests that in addition to plate-to-plate contact, current is trying to flow up the bolt and touching only a handful of thread edges creating severe resistance. If the terminal post was welded or threaded through the baseplate this issue would probably not occur.
I am aware the use of the infrared thermometer on various angled surfaces may create some artifact readings. I played around quite a bit with monitoring different surfaces from different angles, and came up with fairly consistent results.
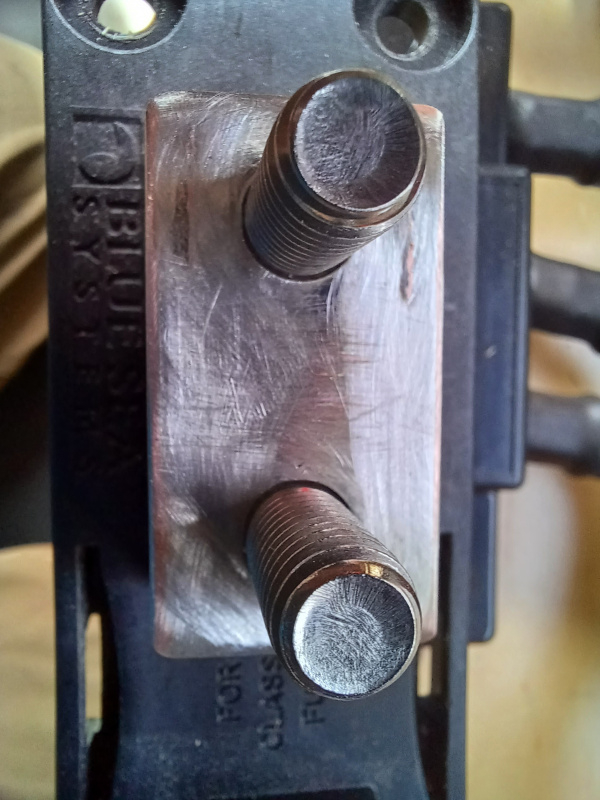
@rfuss928 kindly weigh in on this issue.
Per internet search, there are counterfeit rotary Blue Sea switches however this one appears genuine. No findings on fuse.
Comments
2021 TAB 320 BD (w/new owner having fun)
2021 Jeep Grand Cherokee
Southern Maryland
2021 T@B 320S Boondock/ 2012 Tacoma 4 cylinder truck / 2023 Tacoma 6 cyl. truck
I am not familiar with the particular brand of fuse holders.
My experience with high power connections comes from testing electric vehicle power systems where up to 1000 amp bolted terminations were used. Every time a connection was assembled, all surfaces were cleaned ( even on new parts ) much as you describe. Then, all mating surfaces were coated with a silver filled dielectric grease. Like you, we checked connection temperatures during the first high power runs. Also, we were taking literally hundreds of current and voltage measurements and were quick to notice any unusual losses usually long before any dangerous conditions developed. When you measured the high temperature terminal you should have also been able to measure significant voltage drop across that connection. (Watts = Vdrop X Amps)
The lack of bonding between the stud and plate in the fuse holder should not be of any consequence because when the bolts are properly tightened the clamping force will draw all the mating surfaces together.
Your careful assembly and self checking is extraordinary in the DIY environment. Nice catch and remedy. You may want to get some dielectric grease to help prevent oxidation from developing in your high current connections.
Have fun...
Bob
Yes first test of inverter/ microwave draw was an alarming 127 amps. Quickly found this overheating fuse contact. After cleaning it draws less than 90A.
Still eyebrow raising considering my welder is 150A DC.
Great suggestion to use dielectric grease.
2021 T@B 320S Boondock/ 2012 Tacoma 4 cylinder truck / 2023 Tacoma 6 cyl. truck
Silver filled conductive grease on the other hand would seem to be the product to use.
Ken / 2023 Tab 400 “La Bolita” (29,000+ miles) / 2024 Toyota Sequoia
2025 - 1 Trip - 25 nights - 2 National Parks
https://www.amazon.com/Blue-Sea-Systems-5191-Terminal/dp/B0019ZBTV4/ref=asc_df_B0019ZBTV4/?tag=hyprod-20&linkCode=df0&hvadid=312069228616&hvpos=&hvnetw=g&hvrand=17500863388299196384&hvpone=&hvptwo=&hvqmt=&hvdev=c&hvdvcmdl=&hvlocint=&hvlocphy=1017596&hvtargid=pla-436704268468&mcid=5f24138e8048319cbd29f217a73c1ce6&gclid=Cj0KCQjwzZmwBhD8ARIsAH4v1gXOKAX_4-PGwF_Sq0TVy5sJ_KoVJm8U_WNvk-nrpJlNnEfqCi8-jxsaAiurEALw_wcB&th=1
I see EC trades use the CRC dielectric grease on commercial jobs. It's also on the copper feeders to my home and shop panels, transfer switch, and three phase converter. Inspector will fail aluminum feeders without it. Apparently optional on copper. Maybe we should have used a different product? For now will forego any coatings.
For monitoring, going to relocate my cabled thermometer to near inverter terminals. Used to prove out effectiveness of 12v heat recirculation fans in the rear storage compartments.
Thinking of swapping the remote inverter on/off switch for a timer.
2021 T@B 320S Boondock/ 2012 Tacoma 4 cylinder truck / 2023 Tacoma 6 cyl. truck
How to use dielectric grease
Dielectric grease can be applied to the metal parts of virtually any electrical connection that will be exposed to the elements to serve as a sealant that protects the connection from contamination and corrosion.
Application should be done very carefully, as the grease will cut off the flow of electricity through the connection if some of it is left between the mating surfaces. If you are unsure about how to use dielectric grease, consider talking to your local expert, whether it’s for your car or boat.
Dielectric grease is regularly suggested for incorrect applications in threads on this site. Dielectric grease should be used to keep moisture out of connections, not used in them. Do not put it in the pins on a plug, use it on the housing.
It is not a conductor. It should not (as CRC clearly states) be used on mating electrical surfaces where there is supposed to be conductivity.
So no, a judiciously applied amount is not recommended ever.....
Good idea to clean all the surfaces before assembly though for all the connections.
2025 Honda Ridgeline Black Edition with Redarc Trailer Brake Controller
Blue Sea is not responding to emails or calls about whether this is their coating or a fake.
These 225A may be either a bad batch or counterfeit which raises Q/A issues over whether it will blow when needed.
Blue Sea does not sell retail; just ordered replacements through my local supply house- alerted them to this issue.
2021 T@B 320S Boondock/ 2012 Tacoma 4 cylinder truck / 2023 Tacoma 6 cyl. truck
Your temperature test got me thinking about my system. Not all that different than yours. I have a 2000W inverter and use 2/0 AWG wires throughout.
I did a test a few weeks ago with heating up water (in the microwave) for 5 minutes and monitored wire and connection temperatures.
All of the connections (including the T-Fuse) stayed cool except for two points. The load side of my shunt raised about 40F with the 2/0 wire getting fairly warm to the touch. The second point that warmed up (about the same amount) was the input side of my inverter master ON/OFF switch, also with a 2/0 wire.
I rechecked all the connections and found those two well below the recommended torque values. Tight, but not up to the recommended torque values.
Once I torqued everything to the correct values, I no longer have any temperature increase.
Thanks for your post..I now feel better about my system.
I would recommend anyone running an inverter to conduct the same simple check. You may be surprised what you find...I was.
2021 TAB 320 BD (w/new owner having fun)
2021 Jeep Grand Cherokee
Southern Maryland